Special machining
Fesp Mold is able to satisfy any customer request thanks to the use of cutting-edge machinery combined with technological know-how, which also allows us to create molds that require special processing.
1/2
1/2
Die-sinking EDM
4-axis die-sinking EDM suitable for the construction of cavities with threads or for gears, even those with helical teeth.
Machine with Gantry structure and high-speed Z axis.
Machine with Gantry structure and high-speed Z axis.
2/2
2/2
5-axis electrode milling
Electrode milling in 5 continuous axes with spindle up to 42,000 rpm for the best possible surface finish. Machine servitude with Cartesian manipulator and 100-position magazine for an average autonomy of 72 hours
Fesp Achievements
01
Unscrewing moulds
- Classic unscrewing with threaded shaft retraction involves the Internal construction of shafts with related threads and special racks.
- With advancement of the part using the rotating movement of the threaded pin. Assisted by a sliding plate. Suitable for long pitch threads with large diameters.
02
Multi-cavity moulds
- With multiple unscrewing in series and parallel for medical applications in clean rooms.
- For overmolding with microinjections.
- For high production technical sectors with polymers filled with up to 65% glass fiber.
- Multi-cavity sandwich molds for thin-wall and short cycles (<4 sec) for food application.
03
Multi-material molds
- For press with rotary table.
- With insert loading for multi-station vertical press.
- Translational.
04
Other typologies
- Up-down molds for presses with limited strokes. Movement of one half of the mold on a track to allow the extraction of the part.
- Vacuum injection molds suitable for bio materials with high gas release.
Machinery
We create our products thanks to a machine fleet structured to be extremely flexible ensuring the widest range of possible processes, a large company with artisan quality.
-
1/151/15
GF Mikron Mill P800U
Accuracy of ±2µ thanks to the symmetrical gantry design, with two-hinged rotary table. Large working range combined with high rigidity, ideal for achieving an excellent finishing standard. -
2/152/15
GF Mikron Mill E700U
Flexibility and speed, with a rotary-tilting table with two hinges. Excellent in the preparation of plates thanks to the versatility of the spectrum of processes allowed. -
3/153/15
GF Mikron HSM 600
7 pallets to carry work 24 hours a day even on weekends, with rotary-tilting table. Polymer concrete structure that reduces vibrations and eliminates thermal expansion, guaranteeing top-of-the-range performance. Able to combine milling and grinding on the same machine. -
4/154/15
GF Mikron HSM 400
100-pallet warehouse for small components with dedicated aspirator for graphite processing, up to 4 days of total autonomy 24 hours a day. With rotary-tilting table and 42,000 rpm spindle. Ideal for small pieces and maximum precision machining, with micro tools. -
5/155/15
GF Mikron VCE1000 W Pro
The only 3-axis for roughing larger components. Generous in range of work and great removal power. -
6/156/15
DMG DMU 100 Monoblock
Cantilever machine, ideal for large and heavy pieces. Wide working range and large strokes that allow 5-axis machining with long and non-standard tools. -
7/157/15
DMG DMU 60 Monoblock
Cantilever machine, ideal for small pieces with particular finishes. Extremely versatile and, thanks to the large glass, it allows difficult work under the careful supervision of technicians. -
8/158/15
DMG Gildemeister NEF 400
CNC lathe for technical parts equipped for small productions and precision machining on hardened materials. -
9/159/15
Ingersoll Gantry 800
Die sinking EDM with gantry structure optimized for machining with graphite electrodes, 4 axes. -
10/1510/15
Sodick 600
4-axis wire EDM with linear motors for fast and precise cuts. -
11/1511/15
Delta Synthesis
Tangential grinding for surfaces with large range of work. -
12/1512/15
Millutensil
Die Spotting with tilting surfaces for easy control of all closures, extraction system and all movements. Integrated with wax injector for functional verification. -
13/1513/15
Jung
Tangential grinding with thousandth precision for planes and profiles with magnetic chuck mounted on sine bar. -
14/1514/15
Tacchella U600
Internal external cylindrical grinding. -
15/1515/15
Zeiss
Coordinate measuring machine with software for continuous measurement and adjustable probe, 5 axes. Calipso control integrated with CAD for internal use.
At the cutting edge of technology, capable of providing customers with perfect molds that exceed their expectations.
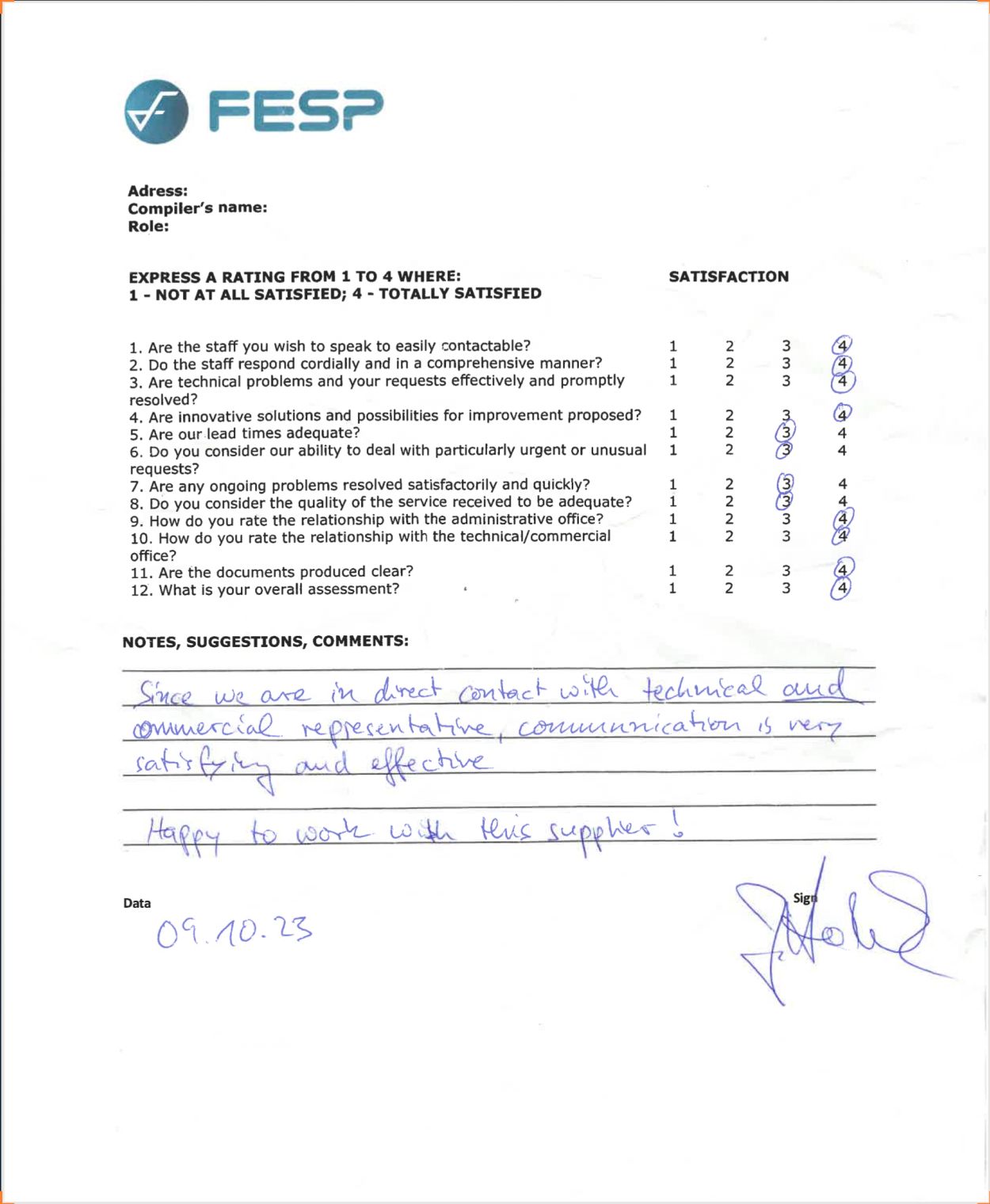
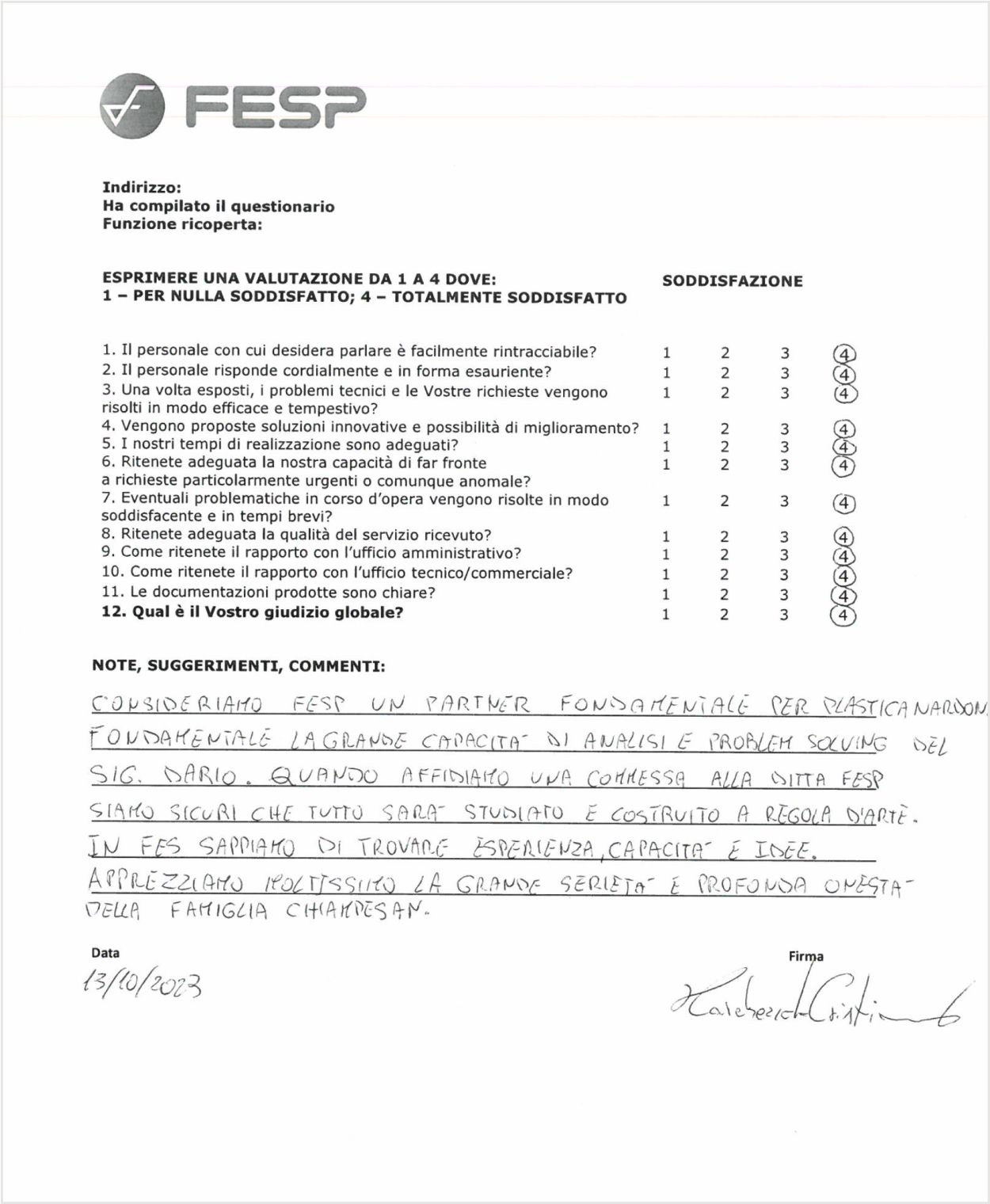
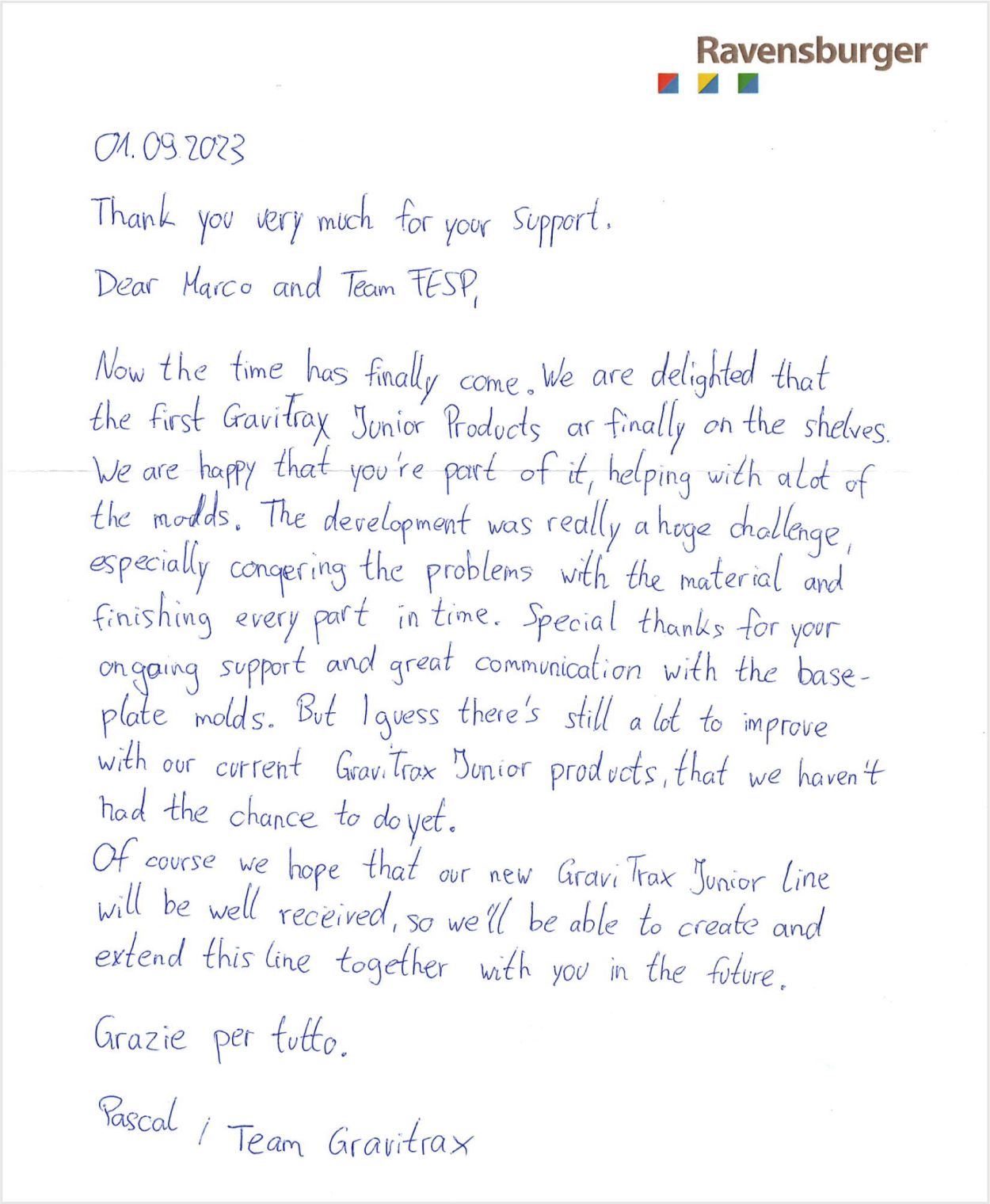
Request a consultancy
-
(+39) 0444 75 07 86
-
(+39) 0444 75 90 35
-
This email address is being protected from spambots. You need JavaScript enabled to view it.
-
FESP MOLD SRL - Construction of molds for plastic materials
Via Meucci, 10 – 36066 Sandrigo (VI)